Como ingeniero especializado en el campo de la refrigeración, me gustaría destacar que las fallas más comunes en las instalaciones con chiller se presentan estadísticamente en el siguiente orden de frecuencia: fugas de refrigerante, bajo flujo de agua debido a la acumulación de sarro y suciedad, fallas en el compresor y fallas en el sistema eléctrico.
Sin embargo, en este artículo abordaremos el estudio de las fallas de un chiller dividiéndolo de la siguiente manera:
- Fallas del Chiller en el Ciclo de Refrigeración.
- Fallas del Chiller ubicadas en el sistema de control.
- Fallas del Chiller originadas en el circuito Hidráulico.
Ahora vamos a estudiar cada clasificación.
Fallas de un chiller en el Ciclo de refrigeración:
- Baja presión de succión en un chiller.
- Compresor con arranque Inundado.
- Refrigerante Líquido en succión de Compresor en funcionamiento.
- Alta temperatura de Descarga.
- Fallas relacionadas con lubricación.
- Fallas en evaporador.
- Fallas en condensador.
Baja presión de succión en un chiller:
Recuerde estas son las principales causas de menor presión de baja en chillers:
- Menor cantidad de refrigerante dentro del circuito de refrigeración, debido a fugas o mal proceso de recarga.
- Menor caudal de agua a través del cooler o evaporador, comparado a la capacidad del chiller.
- Menor carga térmica en la aplicación.
- Estrategia de control del chiller no adecuada, con exceso de número de compresores encendidos.
- Inconvenientes en válvula de expansión o sensores de temperatura.
- Falta de Mantenimiento y mala limpieza del evaporador.
- Baja adaptación del chiller a cargas parciales por valores bajos de IPLV.
MAS Información relacionada con esta Falla:
SOBRECALENTAMIENTO DE EVAPORADOR EN ENFRIADORA
Compresor con Arranque Inundado:
- Al momento de estar apagado el compresor parte del refrigerante del sistema, migra hacia el carter del compresor.
- La migración se produce por la diferencia de temperatura concentración y sobre todo presión.
- El refrigerante desplazado en estado líquido se mezcla o desplaza el aceite del compresor de los puntos que deben estar lubricados.
- Al encender el chiller el lubricante es una mezcla y no aceite puro originando desgastes en piezas vitales.
- Para prevenir esta falla se debe respetar el funcionamiento de las resistencias calentadoras del carter del compresor.
- Se debe respetar el diseño del fabricante, como estrategias de control o sifones.
Información relacionada con modelos de compresores en chillers:
Refrigerante Líquido en succión de Compresor en funcionamiento:
- El refrigerante dentro del ciclo de refrigeración, debe llegar sólo en estado de vapor a la succión del compresor del chiller.
- El refrigerante líquido, no puede ser comprimido por el compresor, y puede causar grandes daños.
- El refrigerante líquido en la succión del compresor, puede ser producto de una estrategia de control no adecuada, como por ejemplo exceso de compresores encendidos.
- El refrigerante líquido en la succión del compresor puede originarse por problemas en la válvula de expansión directamente.
- En chiller más modernos, problemas con sensores, pueden originar estrategias de control no adecuadas en el chiller.
- Para eliminar este problema es vital el buen funcionamiento de la válvula de expansión.
Alta temperatura de Descarga.
Altos valores de temperatura en la descarga degradan el aceite y destruyen propiedades vitales como la viscosidad. Verifique las principales causas de este problema:
- Esta falla puede originarse por alto sobrecalentamiento del gas refrigerante a la salida del evaporador del chiller. Verifique el funcionamiento de la válvula de expansión encargada de graduar el sobrecalentamiento.
- Verifique deterioro del aislamiento de la tuberia de succión del compresor del chiller.
- Conversión inadecuada de gas refrigerante, por ejemplo cambiar el R410A por R32.
- Mal funcionamiento del condensador, esto origina que se eleve la presión de alta, y la temperatura en este punto del chiller.
Fallas relacionadas con Lubricación.
Las siguientes son la causas mas comunes de problemas de lubricación en chillers:
- Verifique modificaciones en trampas de aceite originales del chiller.
- Revizar el sistema de lubricación de estación de compresores.
- Verificar el correcto funcionamiento del separador de aceite.
- Cambio de diametro original de tuberías del chiller.
- Modificación de viscosidad del aceite del chiller,
- Reconversión equivocada de gas refrigerante, que no es compatible con el aceite.
- Falta de aceite.
- Cambio de un modelo de compresor en estación de compresores.
¿Que Falla presenta el Compresor del Chiller según el COLOR DEL ACEITE?
A continuación Vamos a estudiar cada color.
INCOLORO o AMARILLO CLARO.
Indica buen comportamiento
ACEITE NEGRO.
- Indica carbonización causada por aire en el sistema, o la presencia de partículas de desgaste, que contienen hierro.
- Cambie el aceite del compresor y el filtro de aceite.
ACEITE MARRÓN CLARO.
- Use un kit de prueba de ácido para probar la acidez en una muestra del aceite del compresor.
- Cambie el aceite del compresor si la prueba lo indica.
- Indica que superficies de metales diferentes, se han recubierto de cobre, debido a la humedad en el sistema.
ACEITE MARRÓN.
- Indica Aire en el sistema o temperatura alta del compresor.
- Las sustancias químicas pueden causar oxidación, lo que hará que el aceite se vuelva marrón.
- Cambie el aceite del compresor, si la prueba indica que el aceite está ácido
- Una posible causa del revestimiento de cobre, es que a medida que la humedad (agua), se combina con el refrigerante, forma una solución ácida; que puede disolver, o lixiviar el cobre en materiales que lo contienen, como latón o bronce, o el mismo cobre puro.
ACEITE GRIS METALICO.
- Indica la presencia de desgaste, y partículas que contienen aluminio.
- Esto generalmente, es causado por desgaste del cojinete o rayado del pistón.
- El compresor debe ser desmontado. e inspeccionado por componentes desgastados o dañados.
- El aceite y el filtro de aceite deben cambiarse.
ACEITE VERDE.
- El aceite del compresor verde indica que hay agua en el sistema, y es posible que se haya producido un recubrimiento de cobre.
- Se debe desmontar el compresor y el sello del eje.
- Se debe inspeccionar las ruedas, engranajes y rotores.
- Se debe reemplazar, el separador de aceite y debe reemplazarse, y el aceite y el filtro de aceite
¿Cuáles son las averías de un evaporador de un chiller?
Los problemas en el evaporador de un chiller se presentan por:
- Evaporador sucio, con acumulación de sarro que dificulta el intercambio de calor entre el refrigerante del circuito de refrigeración y el agua helada.
- Bajo caudal de agua a enfríar, esto puede ocasionar tendencia al congelamiento del evaporador.
- Baja carga de refrigerante en el ciclo de refrigeración del chiller, puede ocasionar mala calidad del enfriamiento.
- Estrategías de control inadecuadas del chiller, pueden ocasionar exceso o deficit de frio, en el evaporador del chiller.
- Fallas de sensores de temperatura del agua, o del refrigerante del chiller de modo que las estrategpias de control no son las adecuadas.
¿Cuáles son las Fallas del condensador de un chiller?
Dependiendo de la refrigeración de la condensadora, podemos tener:
- Sí la condensadora es refrigerada por aire, se debe verificar velocidad adecuada en los ventiladores.
- La limpieza de las condensadoras es esencial para facilitar el intercambio térmico, se debe verificar el estado de la condensadora.
- Sí la condensadora es refrigerada usando agua se debe verificar la concentración de peliculas de zarro en las paredes del condensador, que afecten el intercambio de calor.
- Deficiencia de la torre de enfriamiento, que impida el correcto acondicionamiento del agua freswca.
Información relacionada con fallas en condensadores:
Fallas de un Chiller ubicadas en Sistema de control.
Fallas en sensores del chiller:
Fallas en los sensores de Temperatura:
- Los sensores de temperatura en chillers frecuentemente son del tipo termorresistencias.
- La termo resistencia tienen la ventaja de emitir una señal lineal con respecto a la temperatura.
- La termo resistencia no se des calibran con facilidad, en caso de daño es más frecuente que queden abiertos, haciendo que el controlador pueda reconocer su fallo rápidamente.
- Una termoresistencia muy usada es el PT1000 .
- El Pt1000 tiene una resistencia de 1000 ohmios a cero grados centígrados.
- El Pt1000 trabaja con valores mayores de resistencia así tenemos la ventaja de tener menos corriente en el circuito, de control, esto hace que puedan generar menos calentamiento y sean más precisos, cuando lo comparamos con el Pt100.
- La longitud del cable o resistencia del sensor Pt1000 Otra característica del pt1000 afecta menos su precisión si lo vemos del punto de porcentaje.
- El Sensor de Temperatura de entrada de agua helada al evaporador, le informa al controlador de la presencia de agua y del valor de temperatura de la misma.
- Sí el sensor de temperatura del evaporador no arrojar valores normales, la unidad se detiene inmediatamente para prevenir daños por no existir los caudales mínimos de agua, requeridos por la máquina.
- La misma estrategia de control sucede, si el problema se presenta con el sensor de temperatura del agua, a la salida del cooler.
- El chiller puede tener un sensor de temperatura en el condensador, para monitorear el proceso y activar estrategías de control, por ejemplo de ventiladores, y manejar el subenfriamiento.
- El chiller puede medir la temperatura del ambiente, para mejorar las estrategias de control del equipo.
- En chillers condensados por agua, se tienen sensores de temperatura a la entrada y salida del condensador, para controlar la velocidad del ventiladores de torre de enfriamiento.
- El sensor de temperatura en la descarga del compresor informa al controlador los valores de temperatura alcanzados por el vapor sobrecalentado a la salida del compresor.
- Para asegurar que un calentamiento excesivo no deteriore el aceite o algún componente del compresor, el controlador supervisa constantemente los valores arrojados por este sensor.
- En algunos chiller el controlador, puede activar la estrategia de enfriamiento del compresor, como por ejemplo inyección de refrigerante líquido.
- Sí el problema de temperaturas de descarga del compresor continua, el controlador procede a detener el equipo, y emitir una alarma. Inmediatamente.
- Se debe enfocar la solución del problema en un Fallo del termistor, solenoide del sistema de refrigeración del motor o algún cableado.
Fallas en sensores de Presión:
- El sensor de presión a la descarga, permite tomar las medidas de control, antes que ocurran los problemas en el chiller.
- El sensor de presión en la succión del compresor, es fundamental para reconocer el sobrecalentamiento del refrigerante a la salida del evaporador del chiller.
- Con la señal del sensor de presión en la succión y el valor de temperatura en este punto, se controla la función de la válvula de expansión electrónica, para el control de caudal de refrigerante.
- Es frecuente la utilización del sensor de presión AKS32 y AKS32R cuya señal es lineal, con respecto a los cambios de presión.
- Para comprobar fallos en el sensor de presión, requiere de multímetro digital para medir voltaje de alimentación y señal, además de manómetro para medir las presiones exactas.
- Para reconocer fallos del sensor debe transformar los valores de voltaje de la señal del sensor, a valores de presión, haciendo uso de la curva del sensor.
- Compare los valores de presión del manómetro con los transformados por el sensor.
- Sí el sensor de presión tanto en succión como en descarga del compresor envié señales fuera de rango al controlador procederá de inmediato a detener el equipo.
- En chillers que trabajen con un sensor de presión como el AKS33 cuya señal es medida en flujo de corriente por ejemplo el sensor AKS33 debemos conocer la curva del sensor, para hacer la comparación con la señal.
Fallas en el circuito Hidráulico:
Aire dentro de tuberías:
- El aire puede introducirse en las tuberías, y afectar el intercambio de calor.
- El porcentaje de aire disuelto en el agua, depende del valor de temperatura y presión.
- Cuando la presión es más grande, el contenido de aire disuelto en el agua es mas alto.
- Con temperatura es más alta, el contenido de aire disuelto disminuye.
- En condiciones de alta temperatura y baja presión este oxígeno se libera en mayor proporción.
- En los cambios de pendientes de las tuberías se producen variaciones de la presión, lo que hace que pueda liberarse aire disuelto con la consiguiente formación de bolsas de aire.
- Las bolsas de aire se desplazan por la tubería y se acumulan en las zonas más elevadas.
- Las bolsas de aire también se acumulan en intercambiadores, afectando su rendimiento.
Inconvenientes con el vaso de expansión:
- El vaso de expansión cuenta con una membrana llena de gas, que puede absorber cambios de volumen del agua, sin afectar el sistema.
- Para evitar fallos, el cálculo de un vaso de expansión es necesario conocer la altura manométrica de la instalación.
- Son de vital importancia para el cálculo las presiones mínima y máxima de trabajo. La presencia de vasos muy grandes o pequeños no logran la función del elemento.
- No es igual el funcionamiento del vaso en el punto más alto que en el sótano, ni antes de los equipos de bombeo que después.
- Obligatorio normativamente, en la línea de alimentación al vaso debe ir instalado un equipo de medición de la presión.
- El vaso de expansión marca el valor de presión de referencia del circuito cerrado.
- No es igual el funcionamiento del vaso en el punto más alto que en el sótano, ni antes de los equipos de bombeo que después.
- En la línea de alimentación al vaso debe ir instalado un equipo de medición de la presión.
Fallos con Bombas en Instalaciones con chiller:
Las intalaciones con chiller requieren de bombas centrífugasm para poder trasladar el agua a través de las tuberías.
- Bombas primarias: Encargadas de enviar el agua al chiller.
- Bombas secundarias: Encargadas de enviar el agua helada, al punto donde se necesita.
- Bombas del condensador: En caso de enfriadoras con condensador enfriado por agua, se requiere un sistema de bombas adicionales, que lleven el agua al condensador y torre de enfriamiento.
Bomba encendida pero sin suministro de agua.
- Verificar que la tubería de succión este completamente llena y no exista presencia de aire en la misma o en el cuerpo de la Bomba.
- Verificar estado de la válvula de pie y obstrucciones en el filtro.
- Si falta agua en la tubería de succión; las bombas vienen provista de una toma para cebarlas.
- Para cebar se debe retirar este tapón y agregar agua hasta que no salga aire y el agua se rebose, si la tubería no se llena se debe reemplazar la válvula de pie.
- Verificar el sentido de giro del motor.
Bajo Caudal de agua.
- Entrada de aire en la tubería de aspiración o a través del sello.
- Si la bomba emplea empaquetaduras reemplazar los cordones si se observa fuga excesiva de fluido.
Sobre Carga en el Motor.
- Equipo fuera de los rangos de operación, verificar estrangulamiento de la válvula de descarga, para disminuir el caudal de la Bomba.
- Daños en los alabes del impulsor, pueden ocasionar desbalanceo y vibraciones que afectan la operación del motor.
- Fallas en rodamientos del motor o eje de bomba.
- Bajo aislamiento en las Bobinas del Motor.
- Desalineación.
Perdida de ceba en Bomba.
- Válvula de pie defectuosa y escapa el agua.
- Perdidas de agua por daños en sellos o empaques.
- Fugas en la tubería o accesorios.
- Entrada de aire en la tubería de succión o fuga excesiva en el área de impulsión.
Falla prematura de Sellos o empaques.
- Desbalance o desalineación.
- Falta de lubricación.
- Verificar que la bomba no esté funcionando en vacío.
Seguramente te va interesar:
¿Necesitas aprender todo sobre chillers?
Mundochiller ha preparado un programa de formación con toda la información que usted necesita sobre las enfriadoras de agua.
CURSO DE CHILLER
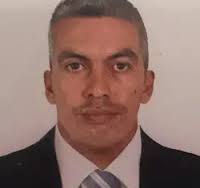
Ingeniero Mecánico con amplia experiencia en diseño, formación, análisis y gestión de proyectos.
http://www.uc.edu.ve/
Miembro activo del Colegio de Ingenieros de Venezuela (CIV)
- Credencial: 131187
- Fecha de afiliación: [05, 2002]
https://www.civ.net.ve/
Mi carrera profesional se ha centrado en el campo de la Refrigeración Industrial y Comercial, donde he desempeñado roles de consultor y formador en diversas organizaciones en Venezuela. He tenido el honor de trabajar con las siguientes instituciones:
Multiskill Consultoría y Formación, con sede en Valencia, Venezuela.
Creaaca Centro de Refrigeración y Aire Acondicionado, ubicado en Caracas, Venezuela.
Conforempresarial, Consultoría y Formación empresarial. Maracay, Aragua,Venezuela.
Mi pasión por la ingeniería mecánica y mi experiencia en el campo de la refrigeración me han permitido contribuir de manera significativa al desarrollo de esta industria en Venezuela. Estoy comprometido con la excelencia en mi trabajo y en la formación de futuros profesionales en esta área.
Si deseas obtener más información o ponerse en contacto conmigo, no dudes en hacerlo a través de la sección de contacto.